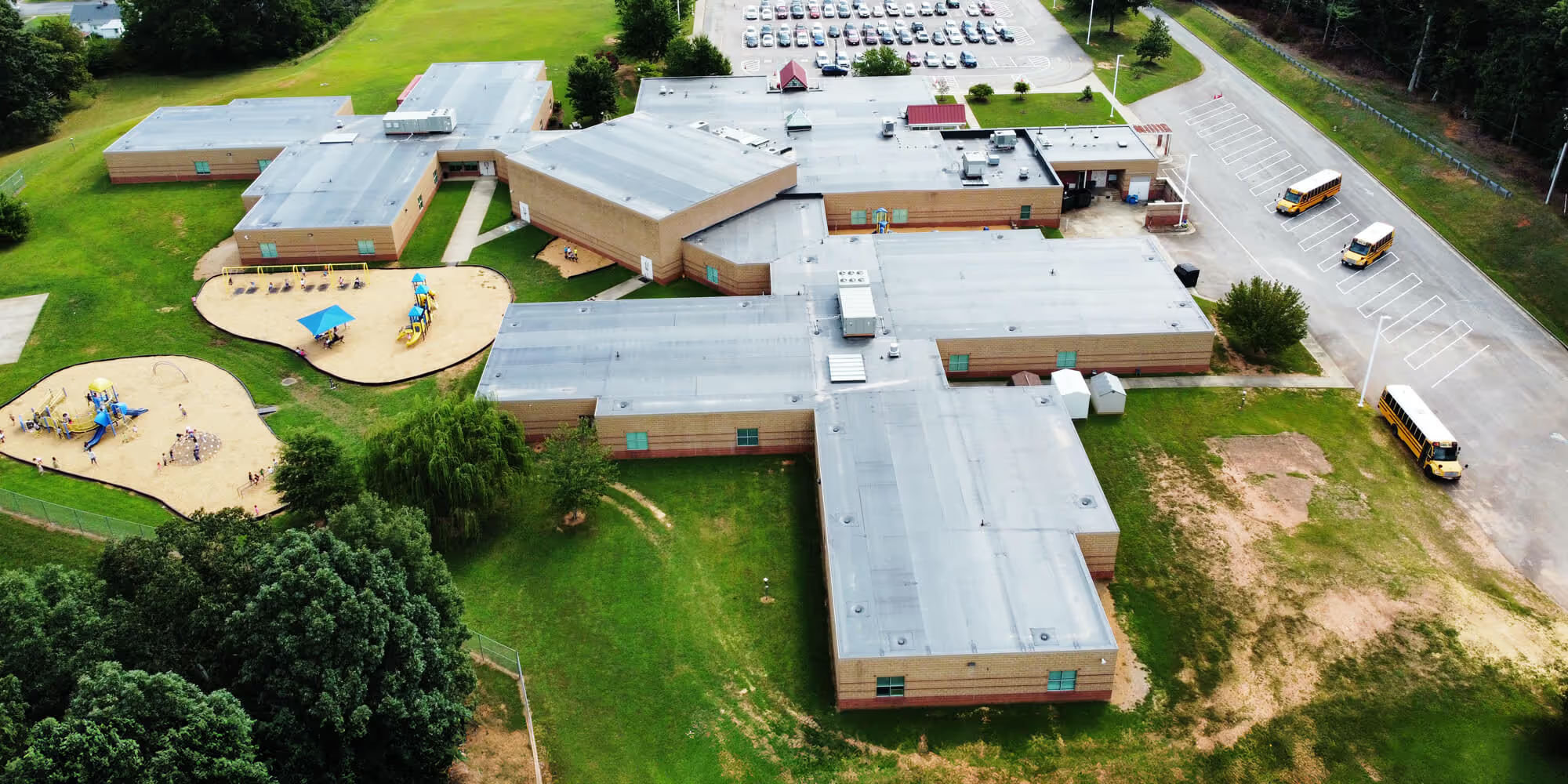
Commercial Roof Inspection
Applied Roofing Solutions is a leading company installing all roofing systems for nearly a decade and a half. We specialize in commercial and industrial properties, offering our clients innovative, cost-effective, and long-lasting roofing solutions. Our team of experts conducts daily inspections and assessments, providing the best recommendations for extending the quality and longevity of your roof.
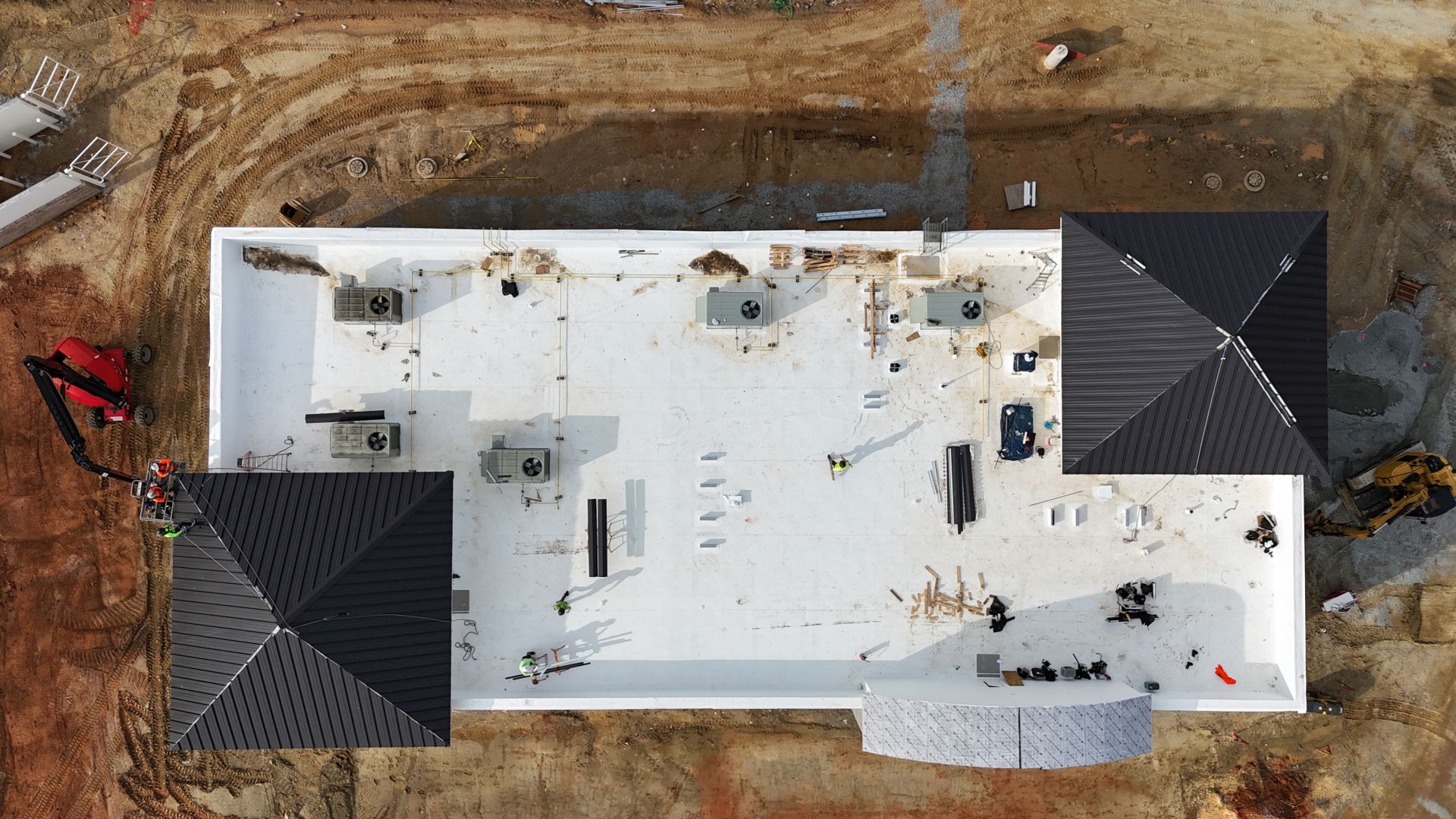
What is the Roof Inspection?
The roofing system is a crucial component of any residential, commercial, or industrial building. Just as it is important to carefully select the right contractor and roofing type during construction, proper maintenance is equally essential. Roof inspections are a professional service offered by authorized applicators of your roofing system’s manufacturer or those dedicated to evaluating roofs' condition, performance, and safety on commercial properties. These inspections help detect potential issues and ensure the roof remains in good, and in many instances warranted condition, preventing costly repairs or major damage.
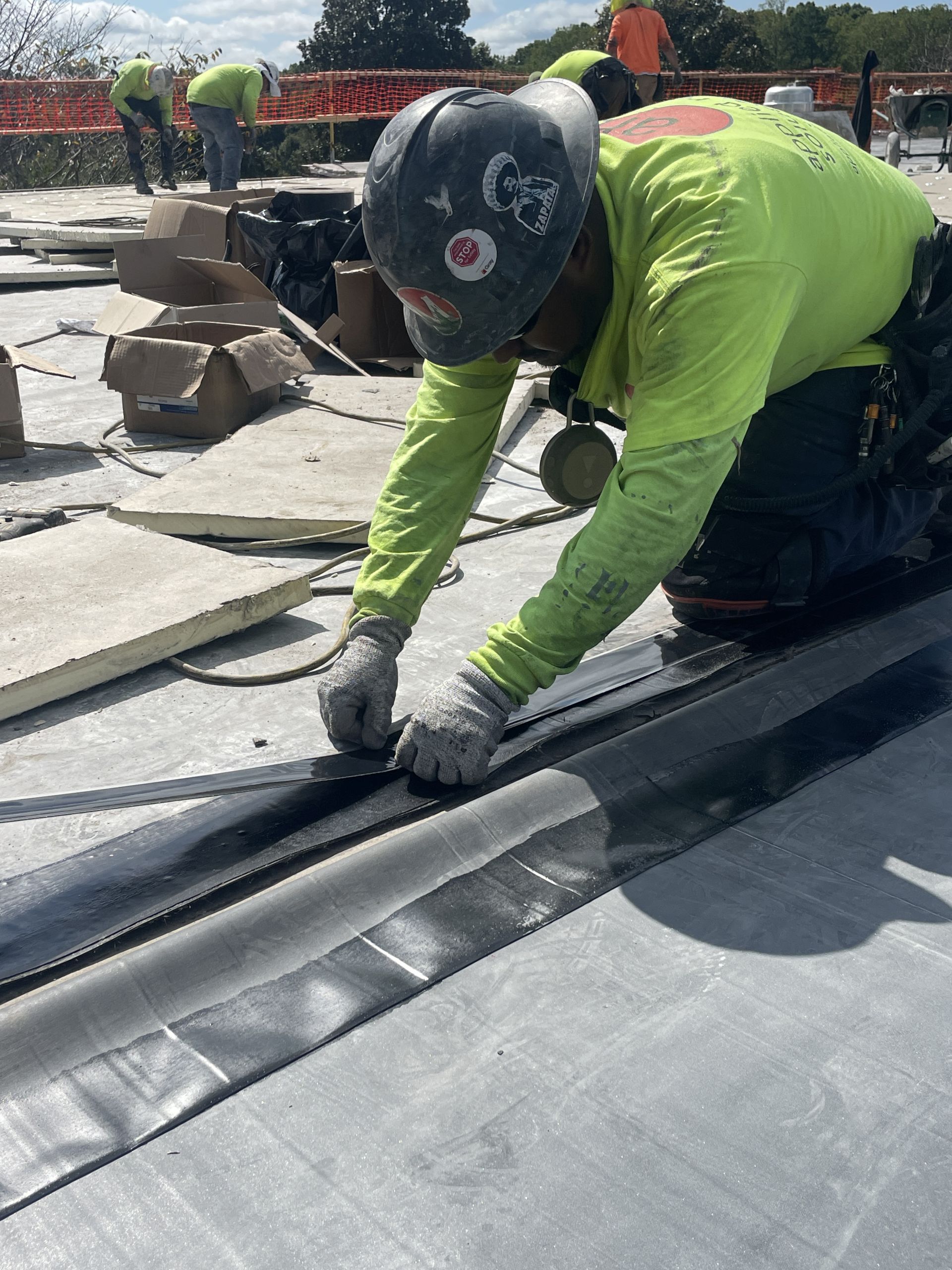
Why is the Inspection Essential?
Investors and building owners often only consider the condition of the roof when a problem arises. However, roof inspections should be an essential part of regular building maintenance. This is not just a preventive measure – conducting inspections regularly helps protect your investment over the long term. Once your roof has reached the end of its service life, inspections can also assist in preparing capital budgets and forecasting reroofing projects.
The primary function of a roof is to protect the building and its contents, which also means safeguarding your entire business. Regular maintenance and roof inspections are essential for this purpose.
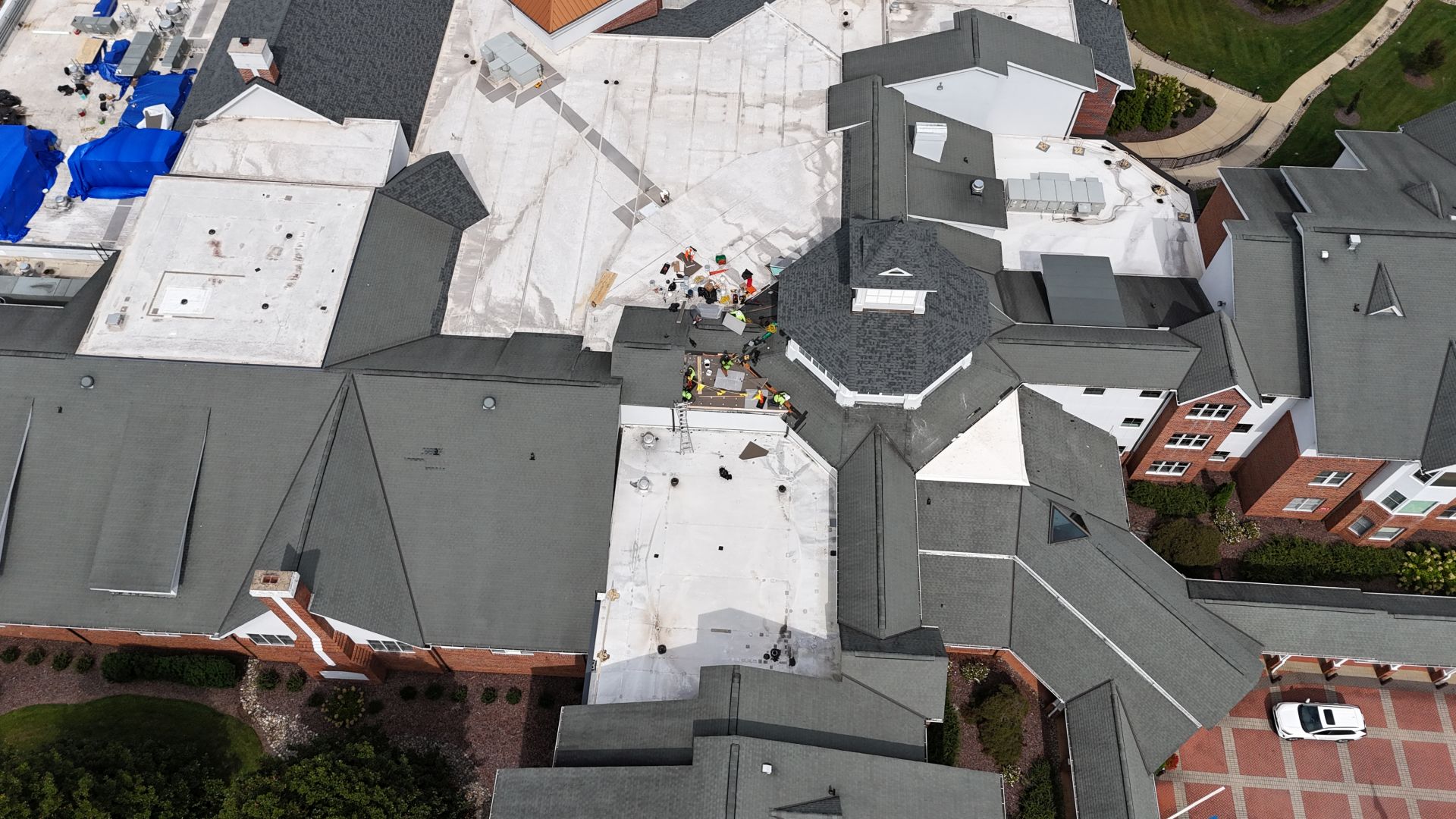
Proactive Damage Prevention
Regular roof inspections of your commercial or industrial property are the best way to protect your investment and your business. Timely identification of issues, such as cracks, leaks, or material damage, allows you to address them early. Detecting minor damage and taking prompt action can prevent larger, more costly problems or system failure. Regular assessments ensure proper roof maintenance, extending its lifespan. This proactive approach saves money by avoiding expensive repairs, emergency interventions, or premature roof replacement. Additionally, unplanned roofing work can cause business disruptions, which can significantly negatively impact your company.
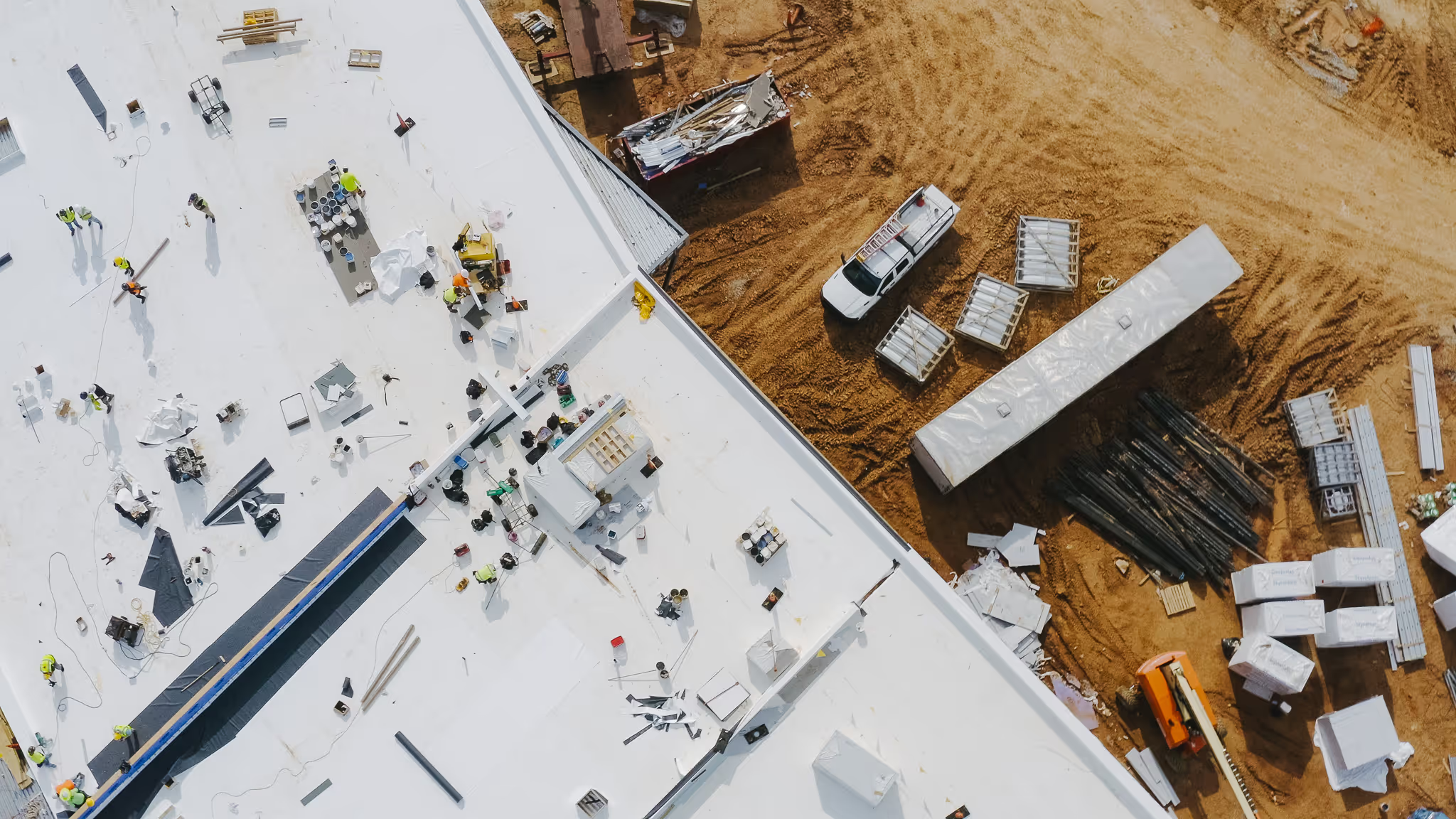
Improved Energy Efficiency
When selecting a roof for any building, energy efficiency is one of the most important factors. It is essential to choose roofing materials that are suitable for the building's intended purpose and appropriate for the local climate. Materials are selected to help maintain an optimal indoor temperature and withstand various weather conditions, whether high heat, harsh snowy winters, or humid environments. Any damage to the roof can lead to increased energy costs. This is why regular inspections are vital, as early detection and repair of issues related to insulation or ventilation can significantly improve energy efficiency and reduce heating and cooling expenses.
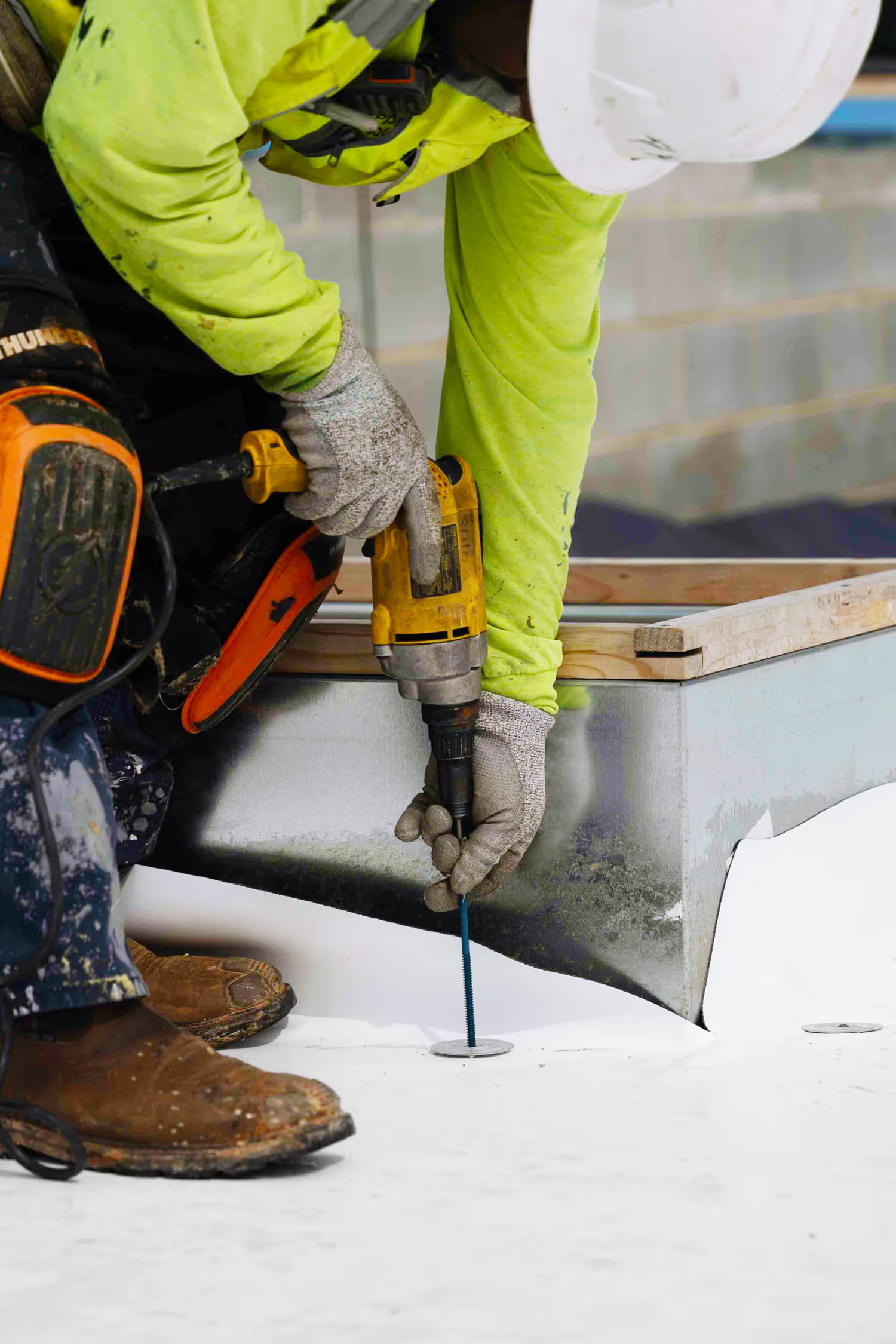
Safety and Compliance
Regular roof inspections ensure the long-term safety of the entire building. Experts in this field will verify that the roof is structurally stable, significantly reducing the risk of leaks, accidents, or collapses that could jeopardize people and property. Additionally, proper maintenance ensures compliance with manufacturer guidelines, keeping warranties valid. Inspections also confirm that the roof meets local regulations and building standards, helping you avoid potential fines or legal issues. Lastly, a well-maintained roof will enhance the property's overall value if you decide to sell or lease it.
Commercial Roof Inspection

TPO Roofing
TPO roof inspections focus on evaluating the condition and performance of this widely used single-ply roofing system. The process ensures that the roof remains durable, energy-efficient, and free from issues that could threaten its stability. The inspection should check the seams for any weaknesses or separation and assess the membrane for signs of wear, damage, or UV degradation. It is also essential to inspect all drainage systems, including gutters, downspouts, and drains, as water retention or slow drainage can lead to long-term damage. The attachment of the membrane to the roof deck should be reviewed, whether it is mechanically fastened, adhered, or ballasted. Additionally, the insulation must be assessed to prevent energy loss due to potential damage.
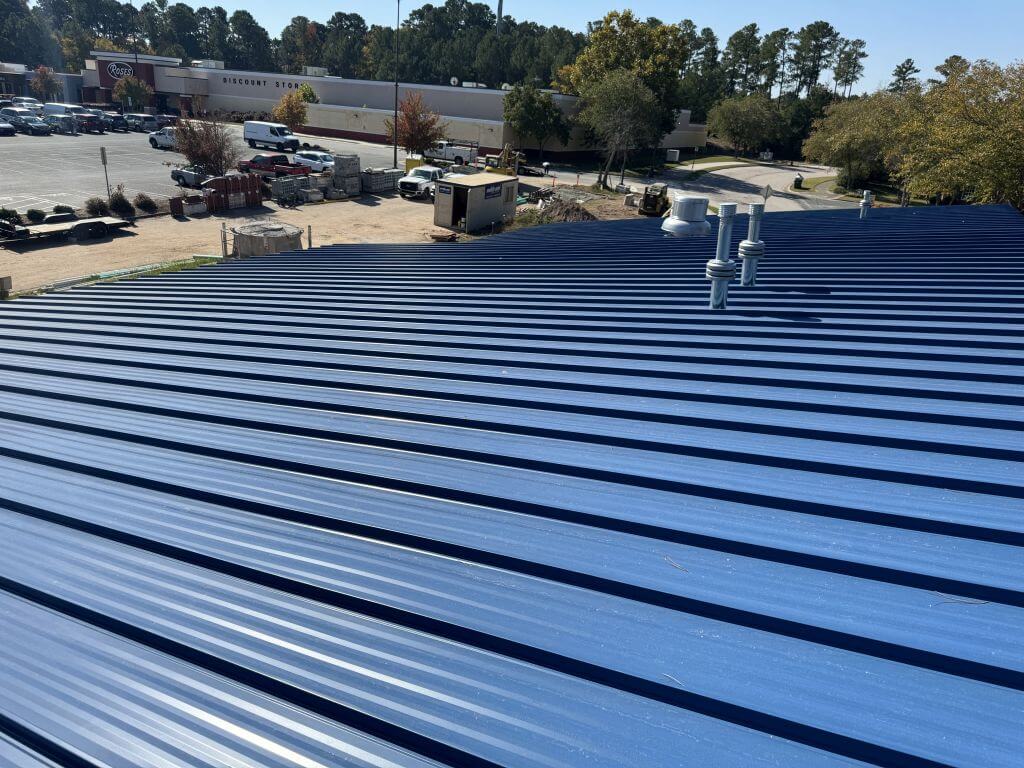
Metal Roofing
During a metal roof inspection, it is essential to thoroughly examine the entire roof structure, checking for drainage or moisture issues, color changes, patch damage, corrosion, or panel displacement. Look for signs of rust or corrosion, especially in moist areas, as rust can weaken the metal and compromise its durability. The inspection should also identify whether any panels are loose or shifted, which could lead to leaks or wind damage. Improper sealing is a common problem with metal roofs, so all seams and joints must be carefully inspected. If damage or installation errors are found in these areas, water infiltration may occur, reducing the overall effectiveness of the roof structure.
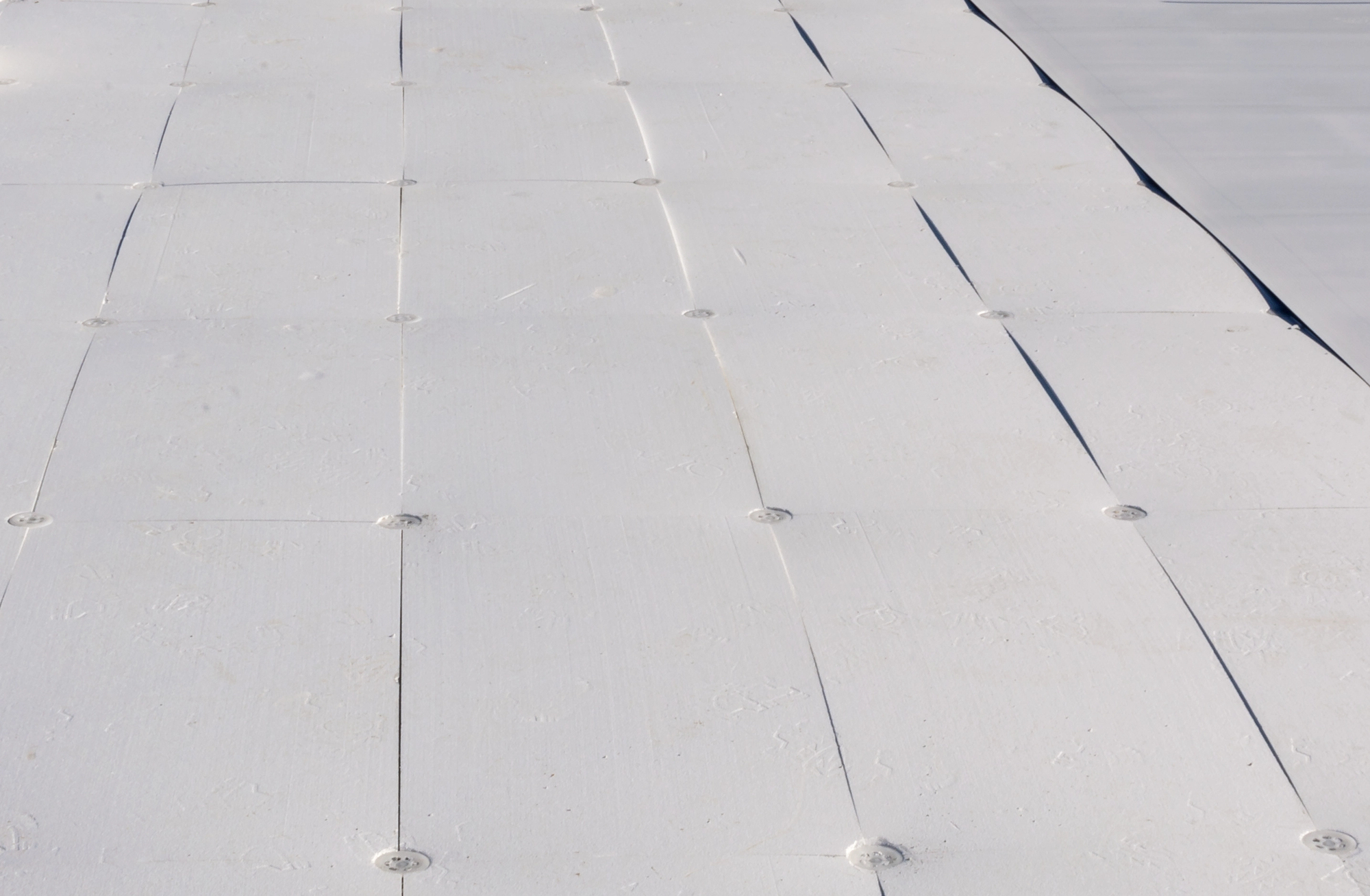
PVC Roofing
PVC roofs are becoming increasingly popular for commercial buildings due to their durability, energy efficiency, and chemical resistance. However, without proper maintenance, they can incur damage. This makes regular inspections essential, with particular attention given to the seams—where two PVC sheets are joined, which are crucial to the overall integrity of the roofing system. One of the primary concerns is the potential separation of seams, which can lead to water penetration and, over time, result in leaks and severe damage.
Additionally, PVC roofs are often heat-welded at the seams, so ensuring the integrity of these joints is vital. Some PVC systems use sealants or adhesives at the seams, making it necessary to assess their condition during inspections to ensure they are still effectively preventing water intrusion.
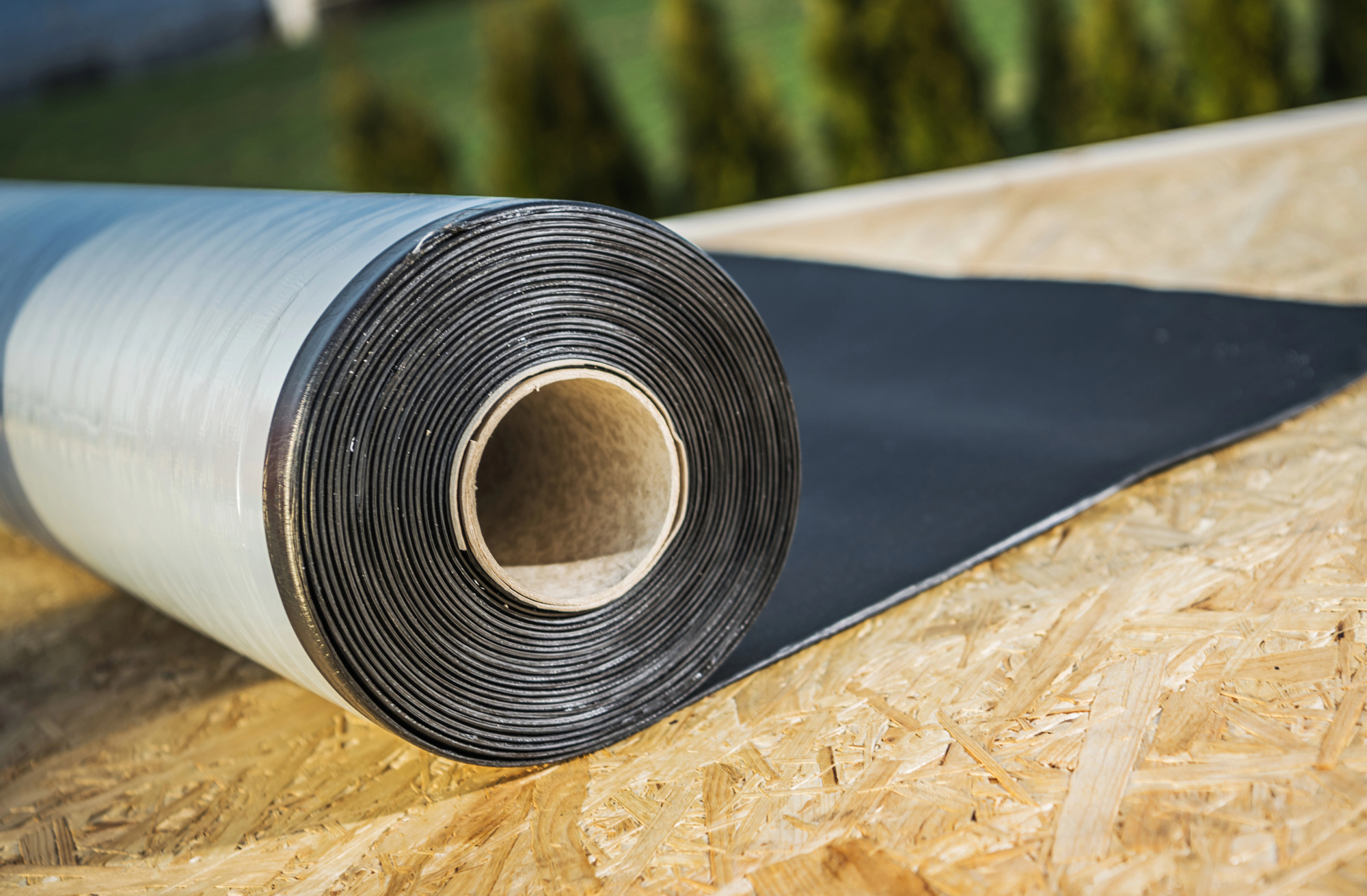
EPDM Roofing
EPDM roofs are renowned for their ability to withstand various weather conditions, including extreme heat, cold, and UV radiation. When inspecting these roofs, special attention should be given to potential cracks, shrinkage, or adhesion issues.
EPDM membranes can develop cracks due to prolonged exposure to weather conditions or physical stress. These cracks may lead to water infiltration, compromising the roof's integrity. Additionally, the material used in EPDM roofs can shrink over time, creating tension at seams, edges, and penetrations, which increases the risk of tearing or separation. EPDM membranes are often attached to the roof deck with adhesive or tape, and over time, parts of the membrane may detach or lift, leaving the roof vulnerable to water leaks and wind damage.
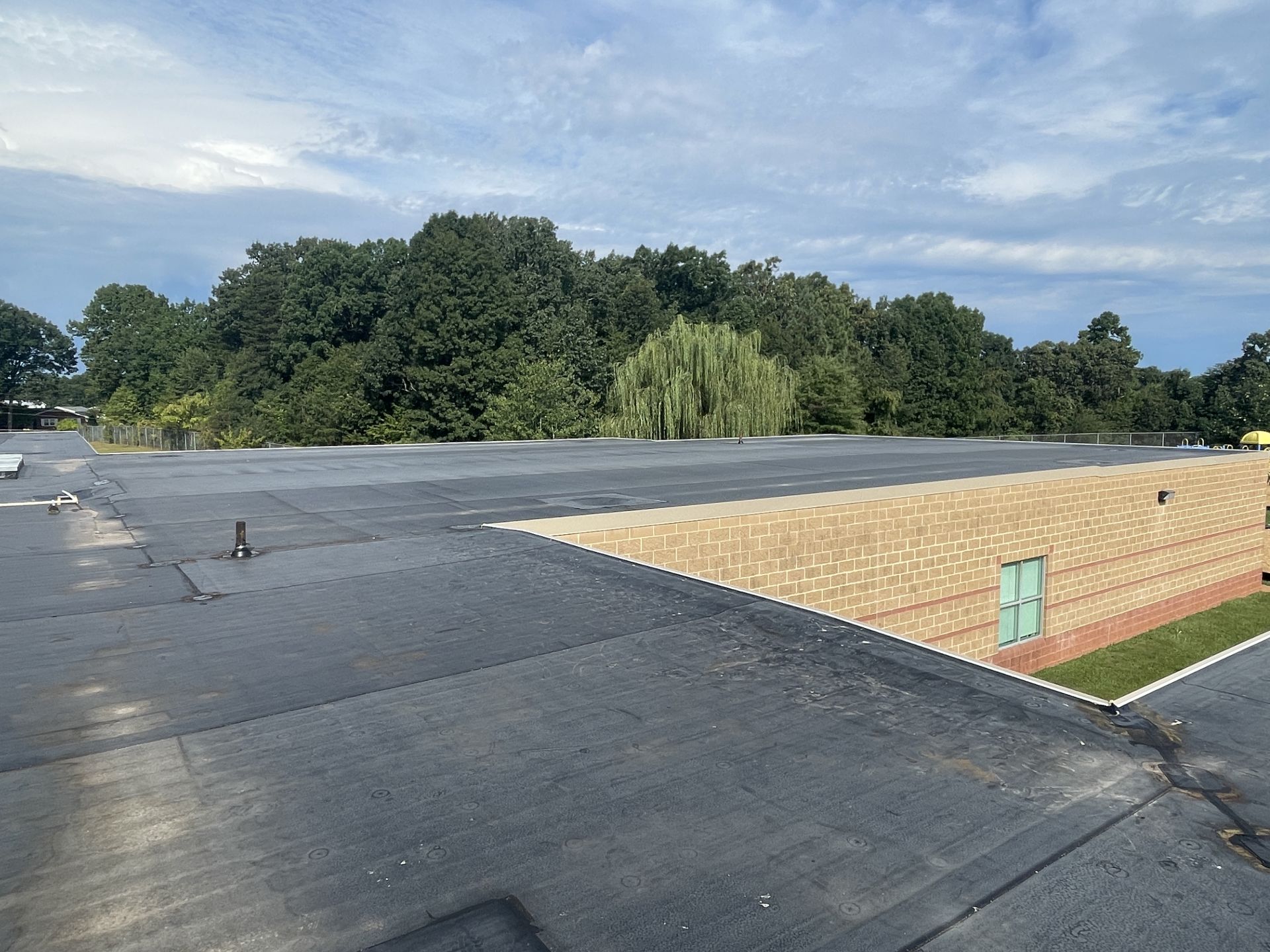
Built-Up/Asphalt Roofing
When inspecting built-up/asphalt roofing, inspectors focus on identifying installation errors and signs of damage and deterioration. Common issues include the formation of blisters, cracks, and wear, particularly in areas exposed to direct sunlight. Blisters may develop due to improper installation or moisture buildup beneath the roof layers. As the roof temperature rises throughout the day, the pressure inside the blisters increases, weakening the bond with the asphalt.
Water accumulation can damage the roofing membrane, degrade the roofing material, cause leaks, and weaken the entire roofing structure. Special attention should be given to inspecting the layers for signs of separation or damage. Additionally, the loss of aggregate from the surface should be checked, as this can reduce the roof's ability to withstand UV radiation and moisture.
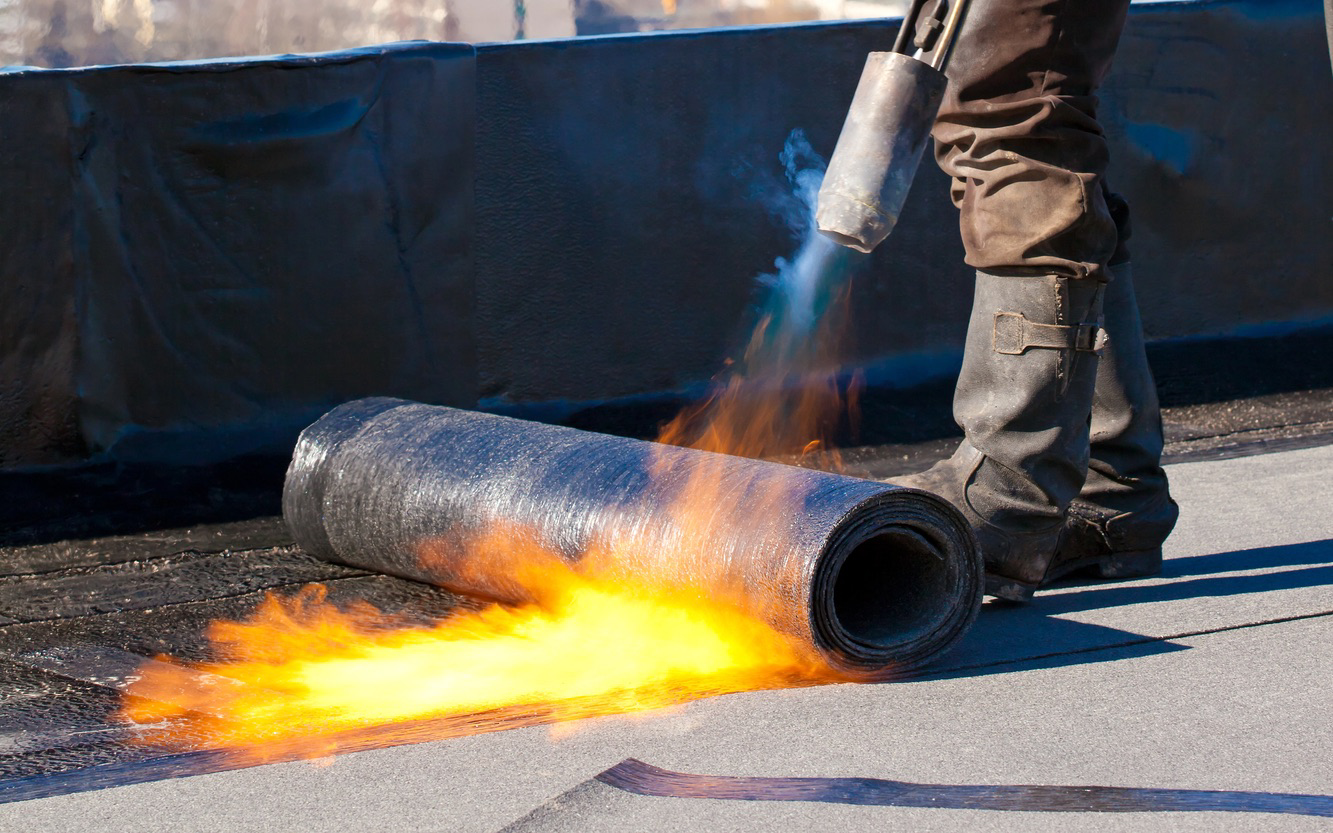
Modified Bitumen Roofing
Modified bitumen roofs are renowned for their durability and versatility, and regular inspections are crucial for the early detection of potential issues that could compromise the roof's performance and longevity. During inspections, it is essential to check for cracks in the membrane, which may result from physical damage, weather conditions, or general wear and tear. Additionally, areas where the membrane is joined should be carefully examined to ensure no separations.
Cracks and separations can allow water infiltration, leading to further damage. Another critical aspect of the inspection is evaluating the surface for signs of granule loss. Granules protect the membrane from UV radiation and environmental elements, and significant loss can reduce the roof's lifespan and make it more vulnerable to damage.
Our Other Services
Applied Roofing offers many other roofing services, including new construction, re-roofing, roof replacement, and commercial roof repair and maintenance.
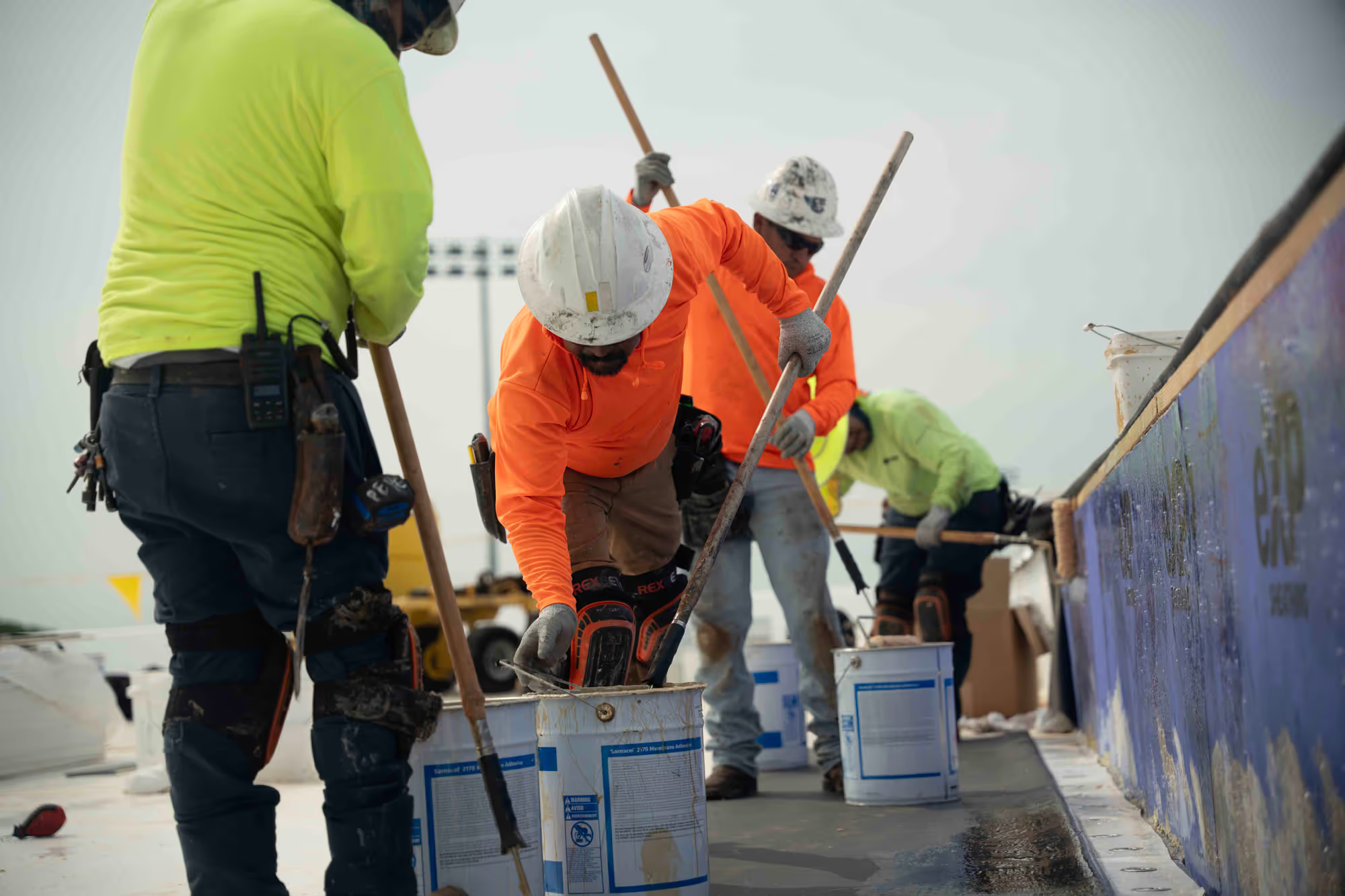
New construction roofing plays a crucial role in the overall durability, functionality, and aesthetic appeal of a building. Unlike re-roofing projects, which involve overlaying or replacing an existing roof, new construction roofing is installed from scratch during the building process. This allows architects, contractors, and property owners to select the most suitable roofing system tailored to the building's design, climate, and intended use. From flat roofs for commercial properties to pitched roofs for residential homes, the choice of materials and techniques significantly impacts the roof's performance and lifespan.
One of the key considerations in new construction roofing is material selection. Options such as metal, PVC, TPO, EPDM, or modified bitumen offer varying durability, energy efficiency, and cost-effectiveness. For instance, metal roofing is ideal for industrial spaces due to its longevity and weather resistance. Similarly, membrane roofing systems like TPO, PVC, and EPDM provide excellent waterproofing, flexibility, and energy efficiency, making them a preferred choice for commercial and industrial applications. Modern advancements in roofing technology, such as reflective coatings and insulated systems, also enable property owners to enhance energy efficiency and reduce long-term operational costs.
Proper installation is equally important in ensuring the roof's effectiveness and longevity. New construction projects benefit from the opportunity to integrate roofing systems seamlessly with other building components, such as insulation, drainage, and ventilation. Working with experienced roofing contractors ensures the roof is installed to meet local building codes and withstand environmental challenges. With the right materials, design, and expertise, new construction roofing provides a solid foundation for the building's protection and functionality for decades. Applied Roofing Services can assist you every step of the way, from design to material selection to installation.
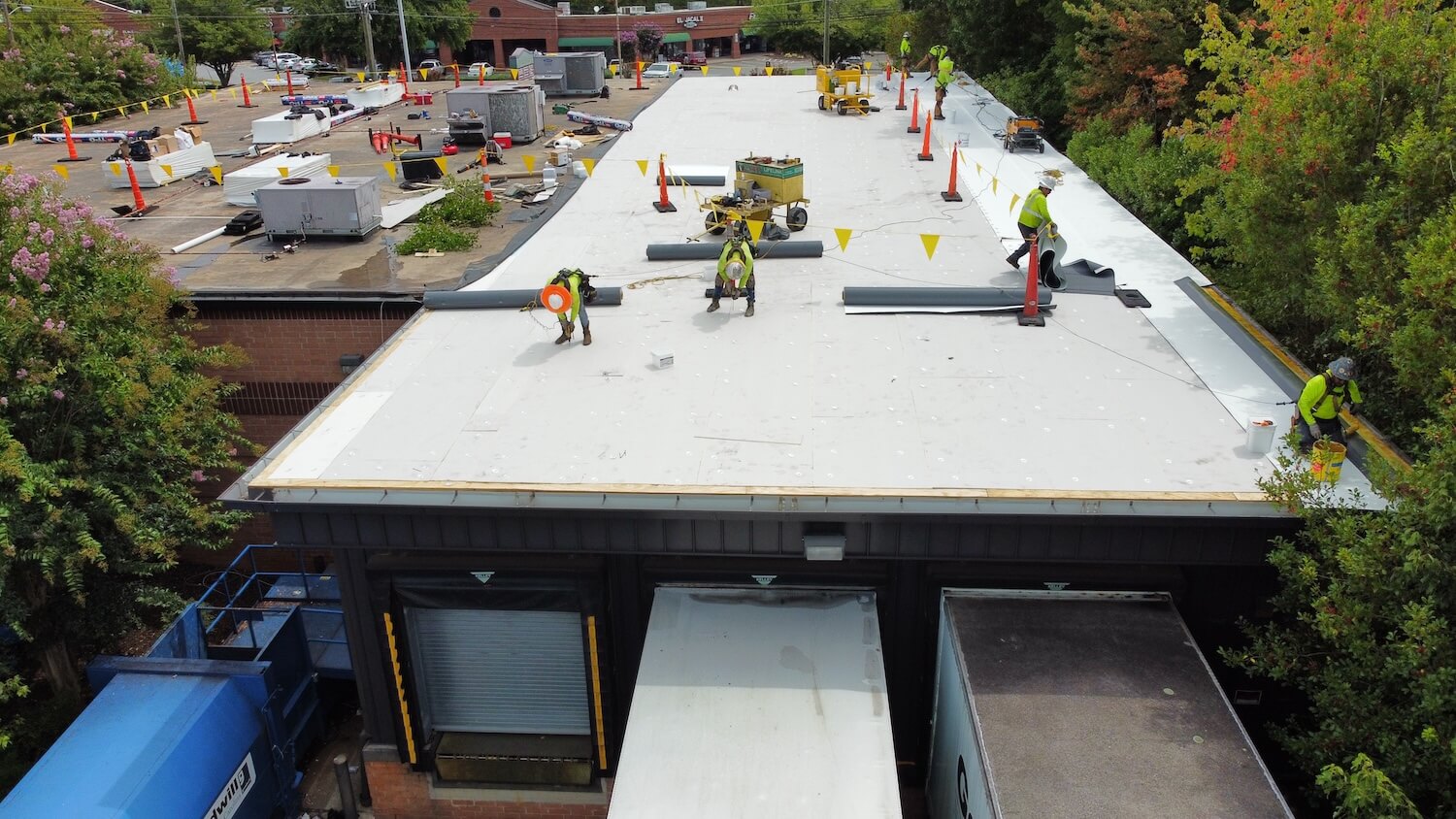
Overlay of Existing Roof System is installing a new roofing layer over an existing one or replacing the old roof entirely. It is a practical solution for addressing leaks, weather damage, or aging materials without a complete roof overhaul. Overlay of existing roof system is often more cost-effective and less time-consuming than new construction roofing, making it a popular choice for property owners looking to extend the lifespan of their roof or improve its performance. However, the feasibility of overlay of existing roof system depends on factors such as the condition of the existing roof, local building codes, and the type of roofing materials being used.
One of the main benefits of overlaying an existing roof system is its ability to enhance the durability and aesthetics of a building. Property owners can address visible wear and tear by adding a new layer of TPO, PVC, EPDM, or modified bitumen, improving the roof’s resistance to weather elements. Additionally, modern roofing materials often incorporate advanced technologies, such as reflective coatings or enhanced waterproofing, which can improve energy efficiency and reduce maintenance costs over time. Overlaying an existing roof system also allows for design or color upgrades, contributing to the property's overall curb appeal.
Working with experienced roofing professionals, such as experts employed at Applied Roofing, is important to ensure proper installation and adherence to local regulations during a overlay of existing roof system project. In some cases, a complete tear-off of the old roof may be necessary to address structural issues or avoid exceeding the roof deck's weight limit. By carefully assessing the existing roof's condition and choosing the right materials and techniques, overlay of existing roof system can provide a cost-effective and efficient way to restore and enhance the functionality of a building's roof. Our engineers and designers can provide expert advice and help you decide.
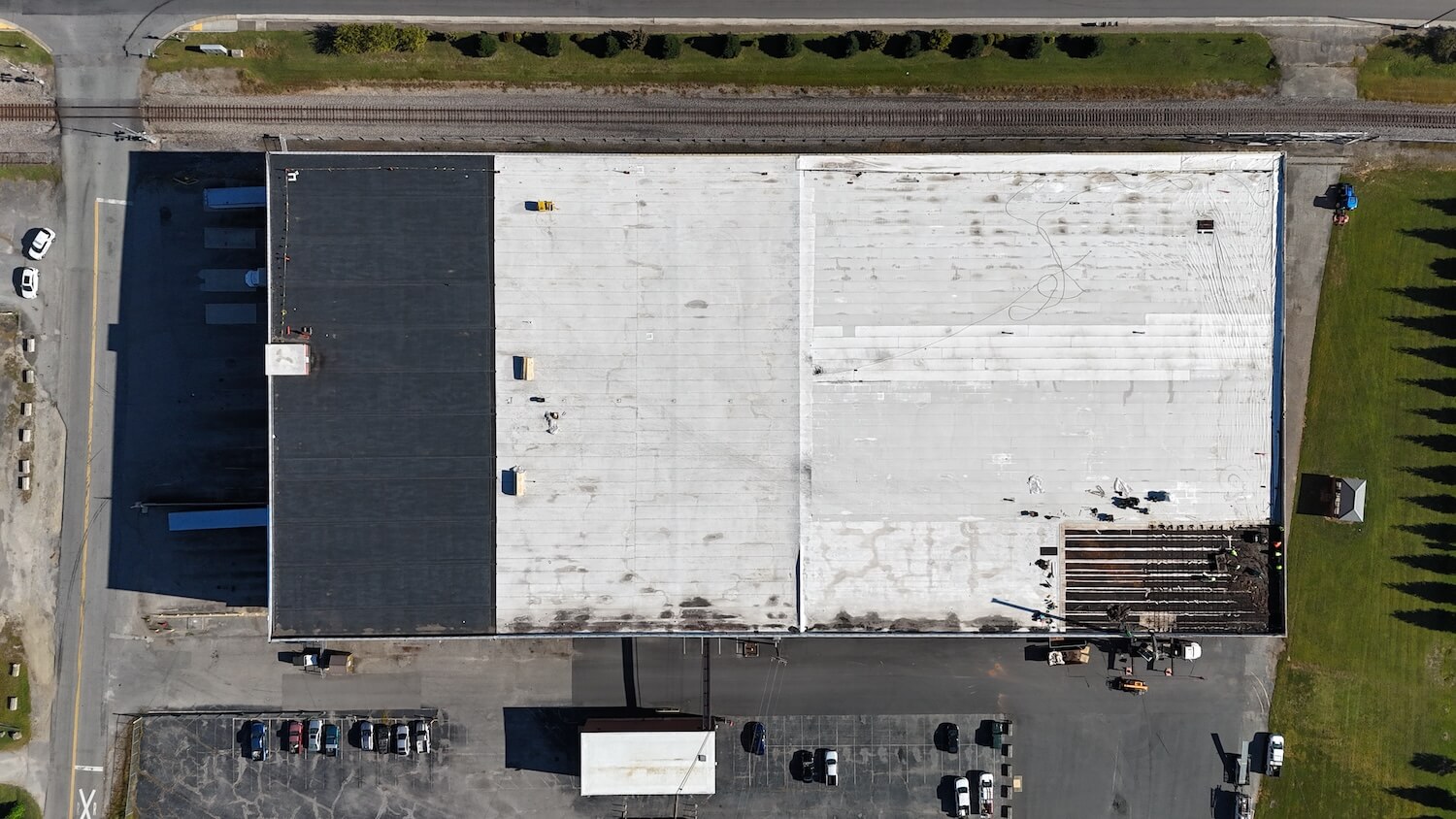
Roof replacement involves removing the existing roof to the deck and installing a new roofing system. This process is often necessary when a roof has reached the end of its lifespan, sustained extensive damage, or is no longer structurally sound. Unlike re-roofing, which adds a new layer over an existing roof, roof replacement addresses underlying issues such as rot, mold, or weakened decking. By starting fresh, Applied Roofing can ensure a safer, more durable roof that meets modern standards and provides long-term protection.
One of the primary benefits of roof replacement is the opportunity to thoroughly inspect and repair the roof deck before installing the new materials. We can address any compromised areas, such as water-damaged wood or deteriorated insulation, to create a solid foundation for the new roof. This comprehensive approach not only enhances the structural integrity of the building but also prevents future problems that could arise from hidden damage. Additionally, Applied Roofing can help you choose from a variety of modern roofing materials, such as TPO, PVC, or EPDM membranes, as well as energy-efficient options, to customize the roof to your specific needs and preferences.
While roof replacement is a more significant investment than repairs or re-roofing, it offers superior durability and peace of mind. A new roof typically has warranties covering materials and installation, ensuring long-term performance and protection. Partnering with experienced contractors such as Applied Roofing is essential for a successful replacement project, as proper installation is key to maximizing the roof's lifespan and function. With the appropriate planning and execution, roof replacement can be a transformative upgrade that adds value, safety, and efficiency to any property.
Process Steps
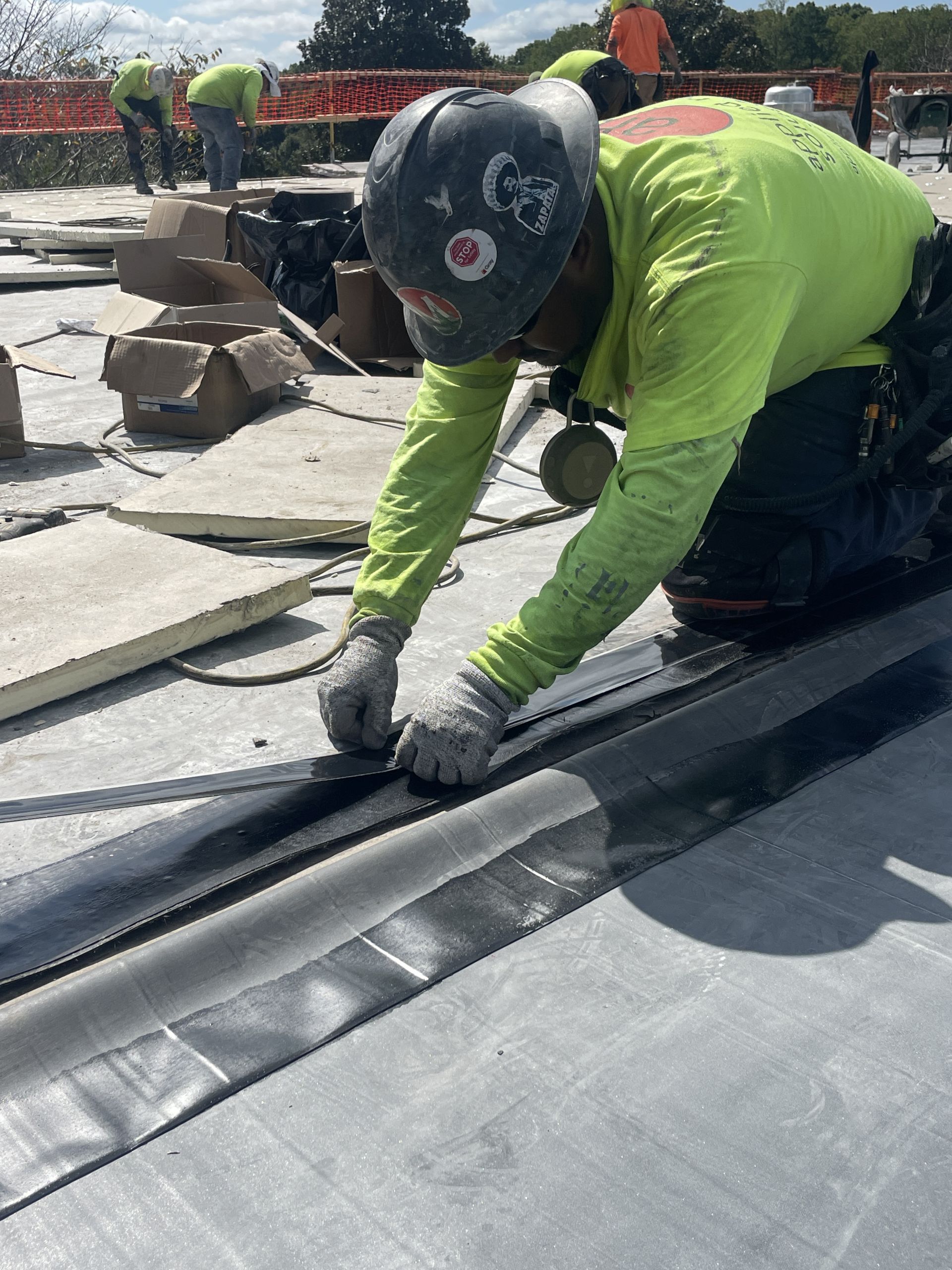
Initial Consultation
The first step in the roofing inspection process for commercial properties is a meeting with the client to discuss the project requirements. This also serves as the initial assessment, where we gather information on the roof's age and repair and maintenance history and review any reports from previous inspections.
.avif)
On-Site Inspection
The next step is a site visit to assess the roof's condition. The exterior is examined for any damage, such as leaks, cracks, water accumulation, and the state of the gutters and drainage system. Structural checks are also performed on the supports, beams, and substrate, as well as an evaluation of insulation, ventilation, and weather-related damage. Additionally, the interior of the building, especially the ceilings and walls, is inspected for signs of water stains, mold, or mildew, which may indicate leaks or damage to the roof.
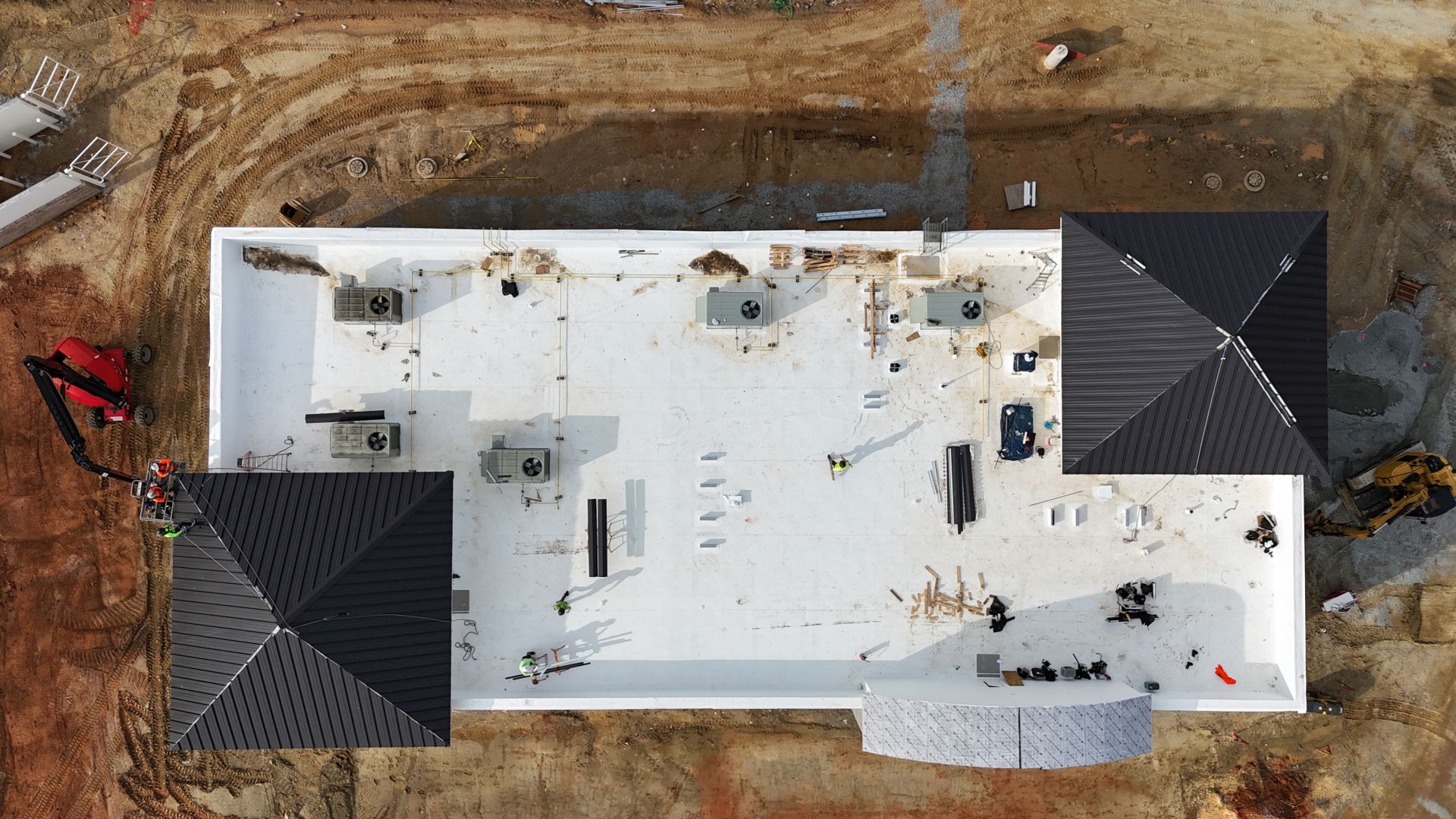
Detailed Reporting
After the inspection, a comprehensive report is prepared, including all relevant information and photographs. The report provides a detailed description of the roof's condition, identifies potential issues, and offers recommendations for repairs or maintenance. It also includes an assessment of the required work or improvements.
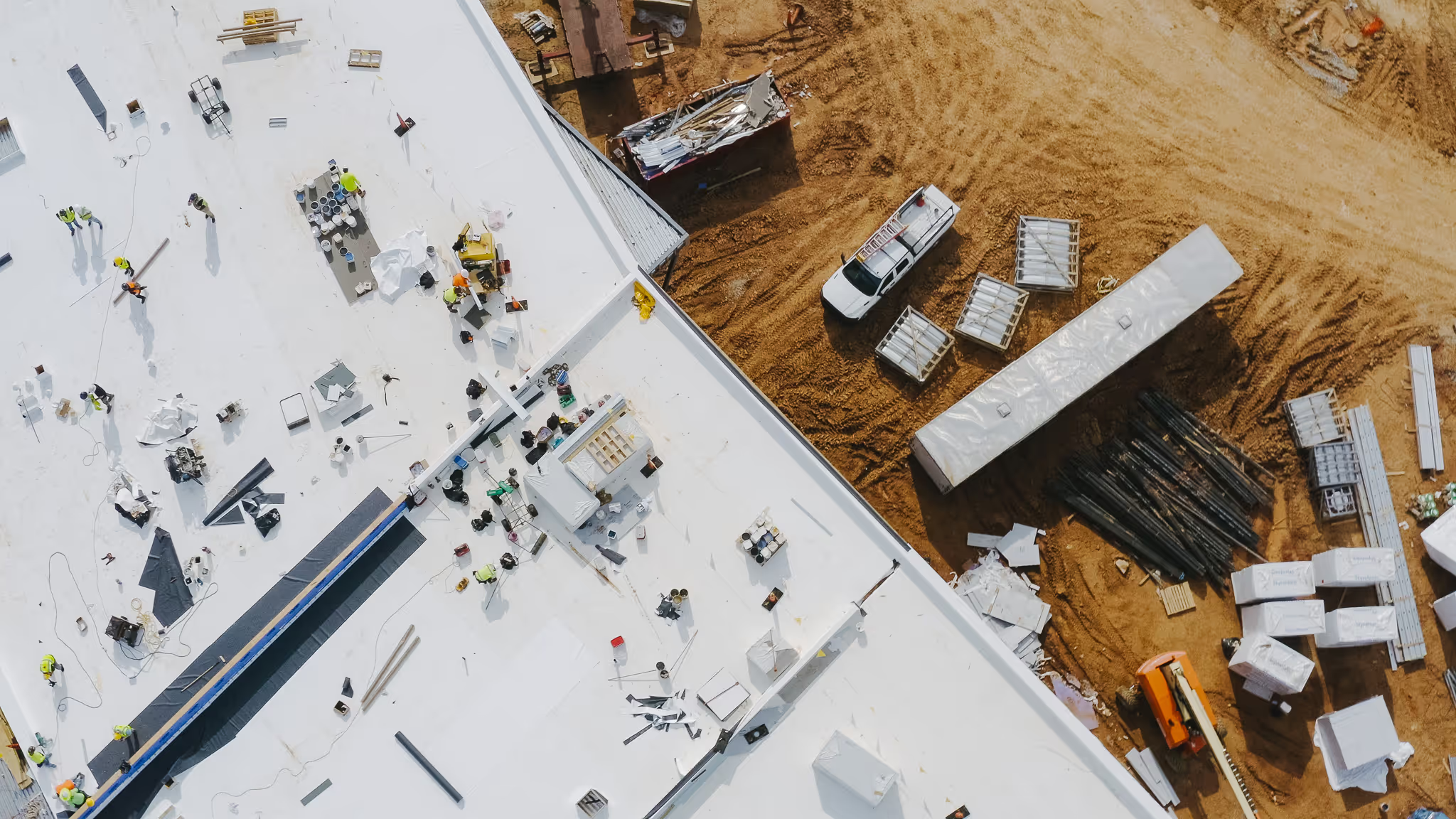
Action Plan Development
In this phase of the process, we meet with the client again to present the inspection results. We highlight any damage found and stress the urgency of addressing the issues. If repairs, improvements, or replacements are necessary, we recommend the most effective solutions.
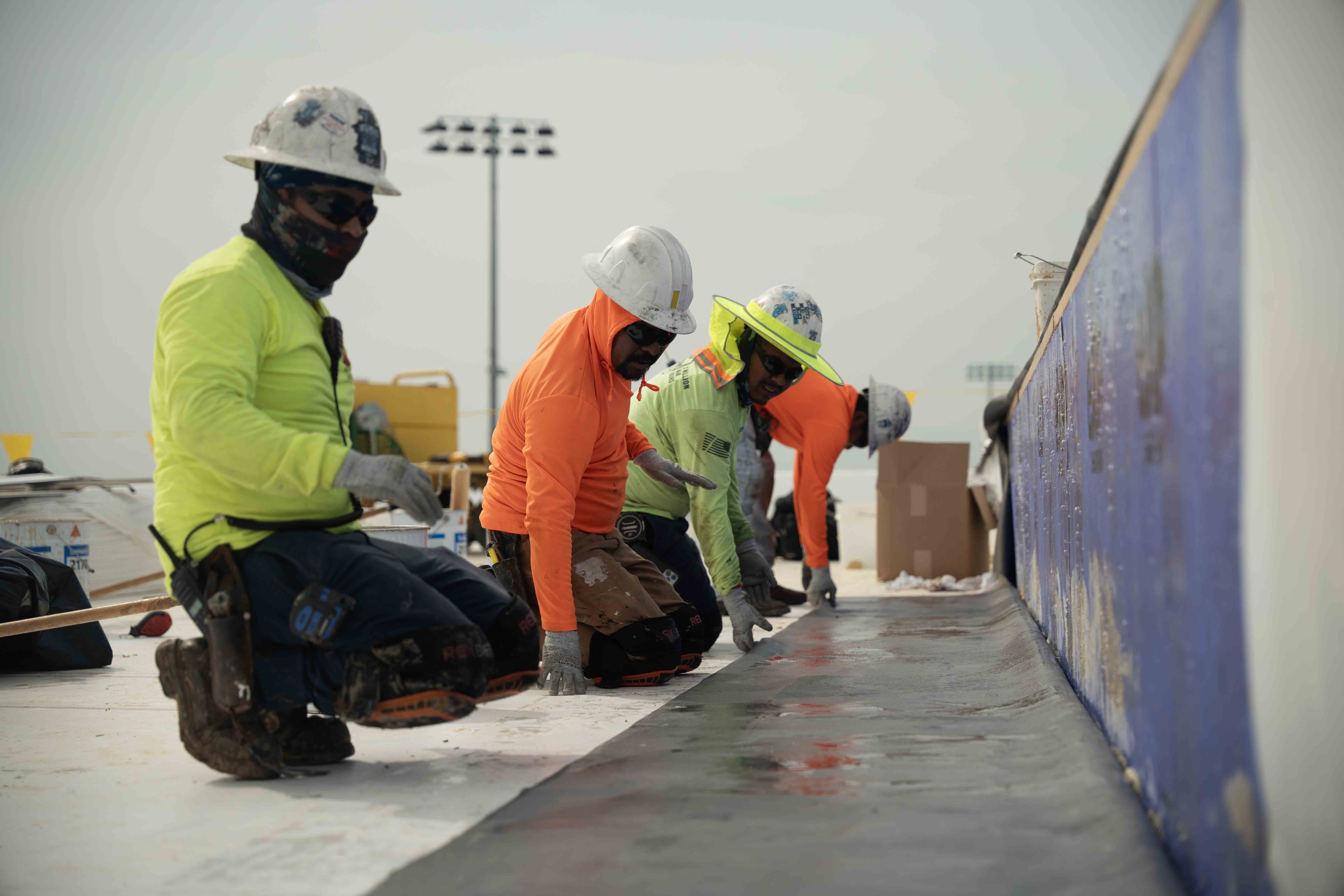
Execution and Follow-Up
If the inspection reveals damage and repairs are needed, our team of experts is ready to take care of this aspect of the project. Once the work is completed, a follow-up inspection will be scheduled, after which a maintenance plan will be developed to extend the roof's lifespan and prevent future issues.
Partner With Us
Our team is ready to support you with any challenges or questions you may have.
What is included in a commercial roofing inspection?
The inspection of commercial roofs includes a thorough assessment to identify any existing damage, followed by examining the roofing components and a structural inspection to check for issues within the roof's framework, including the supporting beams. The building is also inspected to look for signs of roof damage on the ceilings or walls. Afterward, a detailed report is prepared outlining all inspection findings, recommendations for repairs or roof replacement, and maintenance suggestions.
How often should I schedule commercial roof inspections?
Commercial roof inspections should be carried out twice a year, preferably in the spring and fall, to evaluate the roof's condition after the challenging winter and summer weather conditions. It is also advisable to conduct additional inspections after any severe weather event to assess if any damage has occurred.
What are the benefits of professional commercial roof inspection services?
Regular inspections provide an ongoing assessment of your roof's condition, enabling early problem detection and timely action, which helps you avoid expensive and extensive repairs. This proactive approach also extends the lifespan of your roofing system. Furthermore, if the roof is in good condition, you can rest assured that both people and property within your buildings are safe. Additional benefits include improved energy efficiency, compliance with local regulations, and increased property value.
How does an industrial roof inspection differ from a standard inspection?
Industrial roof inspections differ from standard (residential or commercial) inspections in complexity, scope, and specific requirements. Due to the complexity of the roofing systems, they are more specialized, focusing on safety and advanced technology. In contrast, standard inspections address common issues and do not require specialized knowledge or equipment. While commercial roofs use lightweight materials for design flexibility, industrial roofs require durable materials to withstand heavy loads and harsh conditions, especially in steeply sloped structures.
What should I look for in industrial roof inspection reports?
During the inspection of industrial building roofs, you should gather information on the condition of the roof deck, materials, and roofing components, along with recommendations based on the report. The report should provide an overview of the roof's general condition, the roofing structure, and materials, highlight any potential damage, offer insight into the state of the drainage, insulation, and ventilation systems, ensure compliance with regulations, and include visual documentation as well as recommendations for repairs and future maintenance.
Why are industrial roof surveys important for large buildings?
Industrial roof inspections are essential for large buildings to maintain structural integrity, prevent significant damage and costly repairs, improve energy efficiency, ensure compliance with safety regulations, protect assets, and extend the roof's lifespan.
Can a professional commercial roof inspection help lower repair costs?
Absolutely! Regular inspections make it easy to detect minor issues and prevent them from developing into significant problems. This is especially crucial for older roofs, which may have hidden damage. With consistent maintenance and prompt action, you can significantly reduce repair costs.
What are common issues identified during industrial building roof inspections?
Common issues identified during industrial roof inspections include leaks or water retention, damaged materials, faults in the flashing, debris accumulation, structural weaknesses, UV radiation damage, and problems with insulation or ventilation. Regular inspections help resolve these issues promptly, preventing costly repairs and extending the roof's lifespan.